Quality Control
FMT Industry is a company that specializes in producing high-quality sheet metal products, stamping machines, and vending machines. They have been in the business since 2010, and have a reputation for delivering products that meet the needs and expectations of their customers. One of their core values is quality, and they have implemented a rigorous and effective quality control system to ensure that their products are safe, reliable, and consistent.
Quality control is the process of checking and testing the quality of a product or service before it is delivered to the customer. Quality control involves inspecting the raw materials, components, processes, and final products to detect and correct any defects or deviations from the specifications. Quality control aims to prevent errors and reduce waste, rework, and customer complaints.
FMT Industry follows six steps for implementing a successful quality control system¹:
- Define what should be inspected: FMT Industry has clear and detailed specifications for each of their products, such as dimensions, functions, features, and performance. They also have standards for the quality of the raw materials and components they use, such as sheet metal, electronic parts, and vending machine parts.
- Establish inspection points: FMT Industry has identified the critical points in their production process where inspection is necessary, such as incoming material inspection, in-process inspection, and final product inspection. They also have inspection points for their Rebuild service, where they refurbish old vending machines with new parts and components.
- Determine inspection methods: FMT Industry uses various methods to inspect their products, such as visual inspection, dimensional measurement, functional testing, and performance testing. They use appropriate tools and equipment for each method, such as calipers, gauges, meters, scanners, and software.
- Train inspectors: FMT Industry has a team of qualified and experienced inspectors who are trained in the inspection methods and procedures. They also have regular refresher courses and audits to ensure that the inspectors are competent and consistent.
- Record inspection results: FMT Industry records and documents all the inspection results in a systematic and traceable way. They use software to store and analyze the data, such as defect rates, rejection rates, yield rates, and customer feedback. They also use charts and graphs to visualize the data and identify trends and patterns.
- Implement corrective actions: FMT Industry takes immediate action to correct any defects or deviations found during inspection. They also investigate the root causes of the problems and implement preventive measures to avoid recurrence. They also communicate with their customers and suppliers to inform them of any issues and solutions.
By following these steps, FMT Industry ensures that their products are of high quality and meet the expectations of their customers. They also continuously improve their quality control system by reviewing their performance and implementing best practices. FMT Industry is committed to providing you with the best sheet metal products, stamping machines, and vending machines for your business needs.
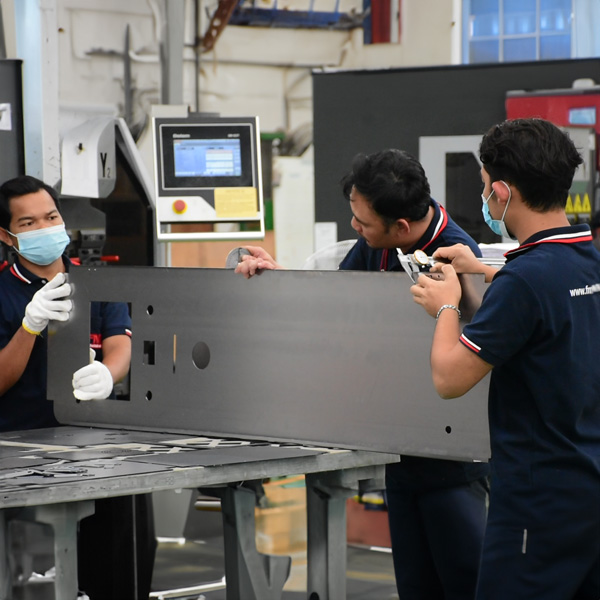
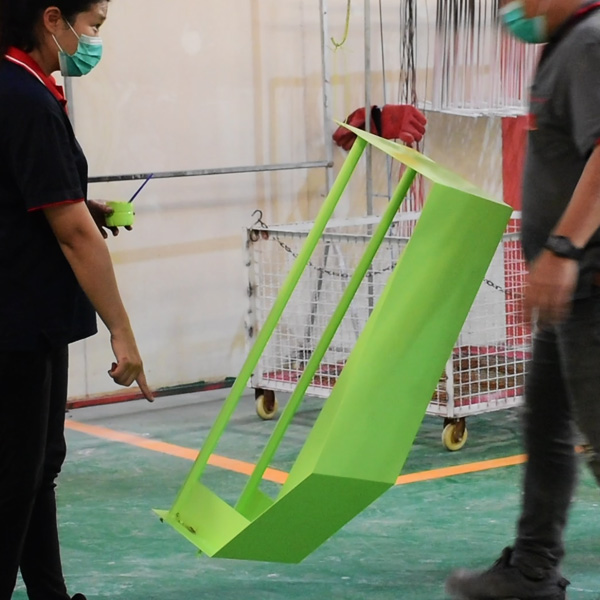
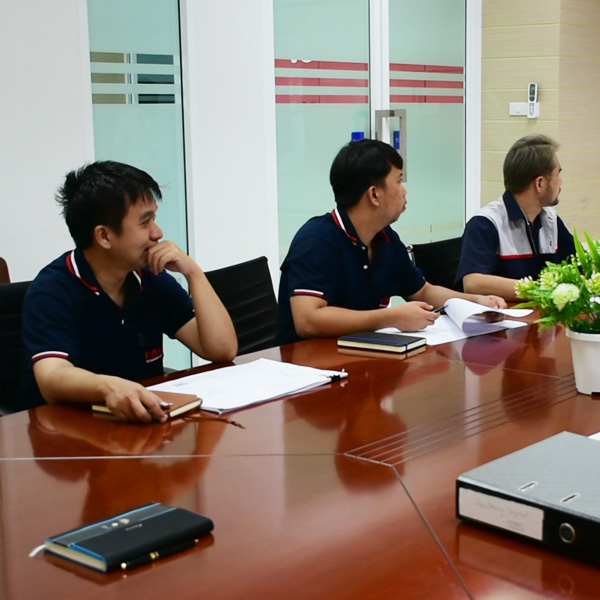
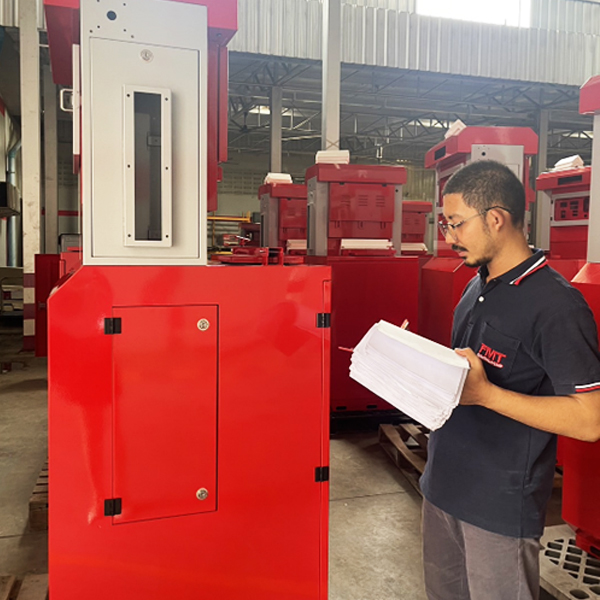